Increasing vaccine thermal stability with PEG-based hydrogels
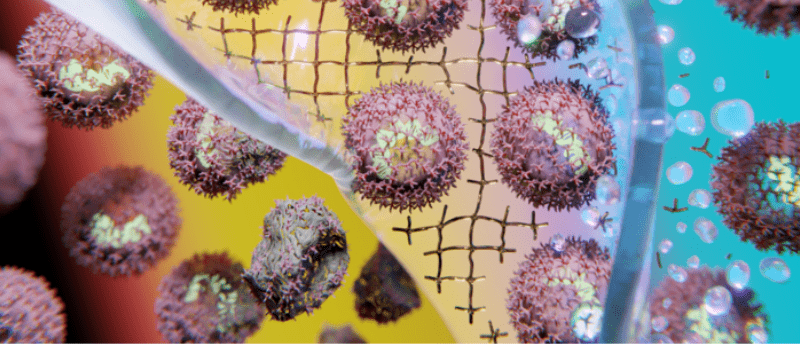
A reversible hydrogel platform has been developed to thermally stabilize biologics, including vaccines, to withstand temperatures up to 65°C.
Nearly half of all vaccines go to waste due to the strict temperature regulation needed throughout the manufacturing process and vaccine administration, meaning they need to be refrigerated to remain effective. Maintaining this constant cold supply chain is challenging even under the most ideal conditions, let alone in regions with limited transport infrastructure and unreliable electricity. To mitigate this, researchers from ETH Zurich (Germany) in collaboration with Nanoly Bioscience (CO, USA) have developed a new hydrogel to package vaccines and increase their thermal stability.
“Think of it [vaccines] like an egg,” explained Bruno Marco-Dufort (ETH Zurich), the first author of this paper. “At room temperature or in the refrigerator the egg maintains its viscous-like protein structure, but once it hits boiling water or the frying pan its structure changes permanently.” Much like an egg, you can’t ‘un-cook’ and reverse the denaturation of proteins in vaccines by cooling them down. So, the research team came up with a packaging system to keep proteins separated and prevent them from clumping together.
The hydrogel is based on a biocompatible synthetic polymer, polyethylene glycol (PEG), that acts like a molecular Tupperware, keeping large complex molecules separated from each other, like the proteins found in vaccines, antibodies and gene therapies.
In vaccines, the PEG-based hydrogel encapsulates proteins enabling them to withstand a higher range of temperature fluctuations by preventing them from aggregating together. Without the packaging, cold chain vaccines tend to withstand a temperature range of 2°C – 8°C (35°F – 45°F). With this reversible packaging system, the temperature range is increased to 25°C – 65°C (75°F – 150°F).
Our top 5 biomedical applications of hydrogels in 2022
Learn more about what hydrogels are and how they’ve been used in drug delivery, 3D tissue models, as a surgical “duct tape” and to create artificial skin.
The hydrogel capitalizes on dynamic covalent bonds, creating a reversible platform that can easily release the proteins from their Tupperware box by adding a simple sugar solution. This means vaccines can be easily recovered at their point of use.
The researchers tested the hydrogel packaging on a variety of biologics, including β-gal, a commonly used model enzyme. The results showed that the enzyme retained more than 90% of its activity after 2 weeks, and more than 75% after 4 weeks of storage in this hydrogel.
“In 2020, the overall market for cold chain services (from manufacturing to distribution) was $17.2 billion and forecasted to rise,” reported the researchers. The rising cost of cold chain manufacturing could have consequences on public health and public trust if vaccines are damaged by compromised cold chains.
The PEG-based hydrogel could yield economic benefits by reducing the costs and health risks that are associated with cold supply chains and mean more funding can be put towards the production of vaccines.
“Most vaccines are sensitive to hot and cold. This creates a large barrier for global immunization campaigns because vaccine distribution and administrative costs often exceed the costs of production,” explained Marco-Dufort.
Before this molecular Tupperware can be rolled out, safety studies and clinical trials are needed. Until then, the technology could be used in a variety of ways including transporting heat-sensitive enzymes used in cancer research or protein molecules in research lab settings.